Mistake-Proof Manufacturing
페이지 정보
작성자 Imogene 작성일25-04-13 20:19 조회3회 댓글0건관련링크
본문
Mistake-yoke, a term used in Japanese, translates to "mistake-preventing" or "defect-free", and it refers to the concept of designing processes and designs that are capable of preventing mistakes from occurring in the first place. This concept is widely used in manufacturing, healthcare, numerous industries, to ensure that errors and anomalies are eliminated and the product or service is of the highest total quality management excellence.
The term Mistake-yoke was first coined in the 1960s by Shigeo Shingo, a renowned Japanese engineer who contributed significantly to the development of the Quality Control Process. Shingo emphasized the importance of designing systems in such a way that they would prevent errors, mistakes, rather than relying on the skill and attention of workers to catch defects.
There are several key principles that guide the design of Mistake-yoke systems:
1. Single Point Defect: One of the primary principles of Mistake-yoke is to ensure that there is only one correct path or way to proceed through a process. This is often achieved by designing a system that will not allow a non-conforming part or faulty component to be processed further.
2. Error Detection: Another principle is error detection or error prevention, which involves incorporating mechanisms that will detect and prevent human defects at each process stage. This could be detected by the use of various sensors, switches, and other devices.
3. Visual Cues: A third principle is the use of visual cues such as signs to help workers perform a process properly. Visual cues can also be used to alert workers of potential hazards such as accidents.
Some common Mistake-yoke techniques include:
1. Alert and Stop systems: These devices interrupt a system or process as soon as a malfunction is detected, thereby preventing any further production or defects adding more anomalies.
2. Go and No-Go gauges: These are devices used to check and verify measurements in a part or component by passing through an intermediary by preventing further progress if the given part is not on the required standards.
3. Tool Change System: This is designed using sensors to avoid miscalculation and ensure smooth change.
4. Double Independent Verification systems: This approach requires that all checks which exist with a double process occur with two independent systems which are then cross-checked for any anomalies or defects to be identified.
Mistake-yoke approaches are widely recognized for being an efficient, sustainable, and cost-effective way to prevent errors and improve quality in various processes. By reducing human mistake, improving productivity in industries, improving efficiency, companies reduce expenses which translate to higher efficiency in the short, medium, and long run.
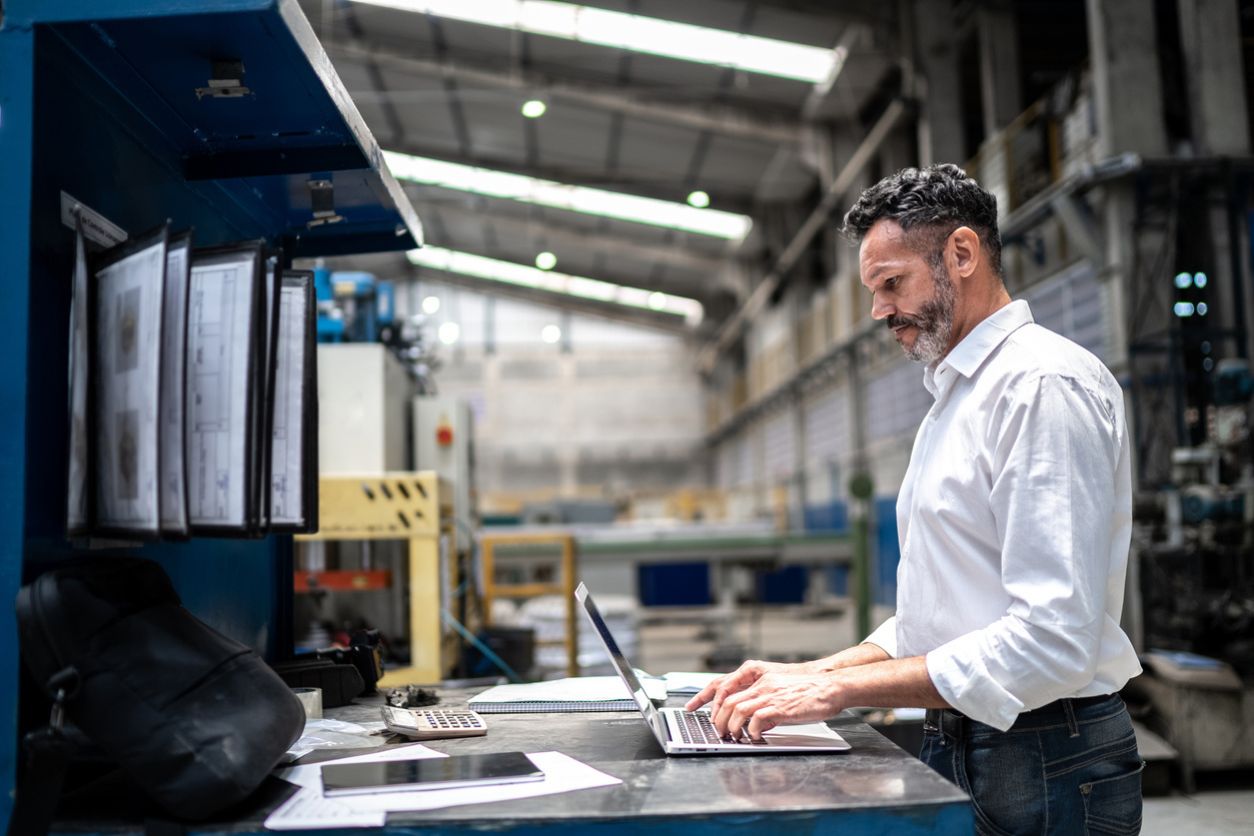
There are several key principles that guide the design of Mistake-yoke systems:
1. Single Point Defect: One of the primary principles of Mistake-yoke is to ensure that there is only one correct path or way to proceed through a process. This is often achieved by designing a system that will not allow a non-conforming part or faulty component to be processed further.
2. Error Detection: Another principle is error detection or error prevention, which involves incorporating mechanisms that will detect and prevent human defects at each process stage. This could be detected by the use of various sensors, switches, and other devices.
3. Visual Cues: A third principle is the use of visual cues such as signs to help workers perform a process properly. Visual cues can also be used to alert workers of potential hazards such as accidents.
Some common Mistake-yoke techniques include:
1. Alert and Stop systems: These devices interrupt a system or process as soon as a malfunction is detected, thereby preventing any further production or defects adding more anomalies.
2. Go and No-Go gauges: These are devices used to check and verify measurements in a part or component by passing through an intermediary by preventing further progress if the given part is not on the required standards.
3. Tool Change System: This is designed using sensors to avoid miscalculation and ensure smooth change.
4. Double Independent Verification systems: This approach requires that all checks which exist with a double process occur with two independent systems which are then cross-checked for any anomalies or defects to be identified.
Mistake-yoke approaches are widely recognized for being an efficient, sustainable, and cost-effective way to prevent errors and improve quality in various processes. By reducing human mistake, improving productivity in industries, improving efficiency, companies reduce expenses which translate to higher efficiency in the short, medium, and long run.
댓글목록
등록된 댓글이 없습니다.