Manufacturer Quality Metric: MQM
페이지 정보
작성자 Lazaro Glynde 작성일25-04-13 19:08 조회2회 댓글0건관련링크
본문
Overall equipment effectiveness is a critical metric for iso consulting services firm manufacturers looking to increase their efficiency. Developed in the 1980s by Seiichi Nakajima, overall equipment effectiveness is now a widely used standard for measuring the effectiveness of manufacturing equipment.
The overall equipment effectiveness metric takes into account four vital elements: availability, efficiency and output. Each of these components affects the final outcome. Deficiencies in any aspect can significantly affect the manufacturing process.
Availability, or plant availability, measures the proportion of operation that production is underway. This not only includes the time when the production is running but also accounts for planned downtime. Availability is heavily impacted by various aspects such as production planning and maintenance procedures.
Performance measures the rate at which a piece of equipment produces at highest efficiency. This metric considers the factory's production volume and operating speed. To assess efficiency, manufacturers determine the actual production of the plant to its operational limits.
Quality is perhaps the most critical component of OEE, as it represents the proportion of output that are produced to meet specifications. High-quality output not only improves the manufacturer's reputation but also reduces losses due to wasted materials. Quality is affected by several elements including operator training.
In assessing overall performance, manufacturers merge data from these areas. When provided with this information, managers can effortlessly detect points of inefficiency within their manufacturing processes. Addressing these issues can have a tangible impact on overall efficiency and ultimately, profitability.
In practical terms, an OEE value of 85% is generally considered competitive. However, manufacturers striving for excellence in manufacturing will strive for OEE values of 90% or higher. By implementing targeted improvements, manufacturers can drive sustainable growth and efficient growth in their businesses.
For OEE to be an useful indicator of efficiency, manufacturers must adopt a data-driven approach to collecting and analyzing metrics. Continuous evaluation of overall performance provides insights for the implementation of necessary improvements, ultimately driving efficiency, product quality, and sustainable development.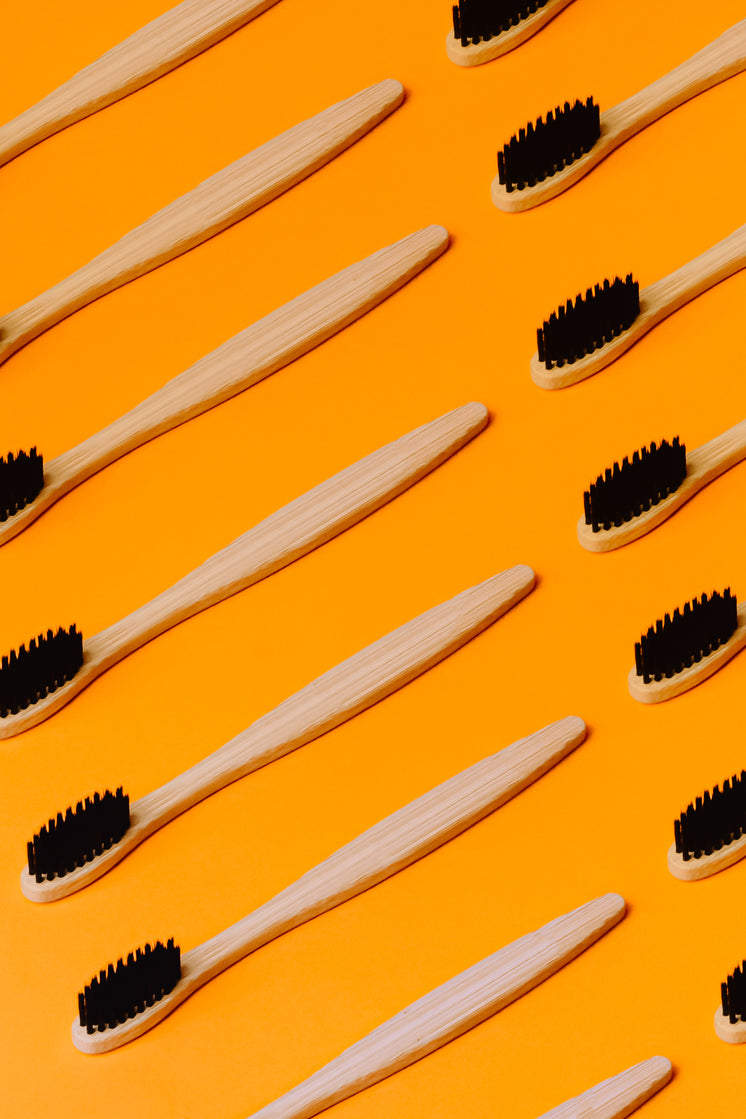
The overall equipment effectiveness metric takes into account four vital elements: availability, efficiency and output. Each of these components affects the final outcome. Deficiencies in any aspect can significantly affect the manufacturing process.
Availability, or plant availability, measures the proportion of operation that production is underway. This not only includes the time when the production is running but also accounts for planned downtime. Availability is heavily impacted by various aspects such as production planning and maintenance procedures.
Performance measures the rate at which a piece of equipment produces at highest efficiency. This metric considers the factory's production volume and operating speed. To assess efficiency, manufacturers determine the actual production of the plant to its operational limits.
Quality is perhaps the most critical component of OEE, as it represents the proportion of output that are produced to meet specifications. High-quality output not only improves the manufacturer's reputation but also reduces losses due to wasted materials. Quality is affected by several elements including operator training.
In assessing overall performance, manufacturers merge data from these areas. When provided with this information, managers can effortlessly detect points of inefficiency within their manufacturing processes. Addressing these issues can have a tangible impact on overall efficiency and ultimately, profitability.
In practical terms, an OEE value of 85% is generally considered competitive. However, manufacturers striving for excellence in manufacturing will strive for OEE values of 90% or higher. By implementing targeted improvements, manufacturers can drive sustainable growth and efficient growth in their businesses.
For OEE to be an useful indicator of efficiency, manufacturers must adopt a data-driven approach to collecting and analyzing metrics. Continuous evaluation of overall performance provides insights for the implementation of necessary improvements, ultimately driving efficiency, product quality, and sustainable development.
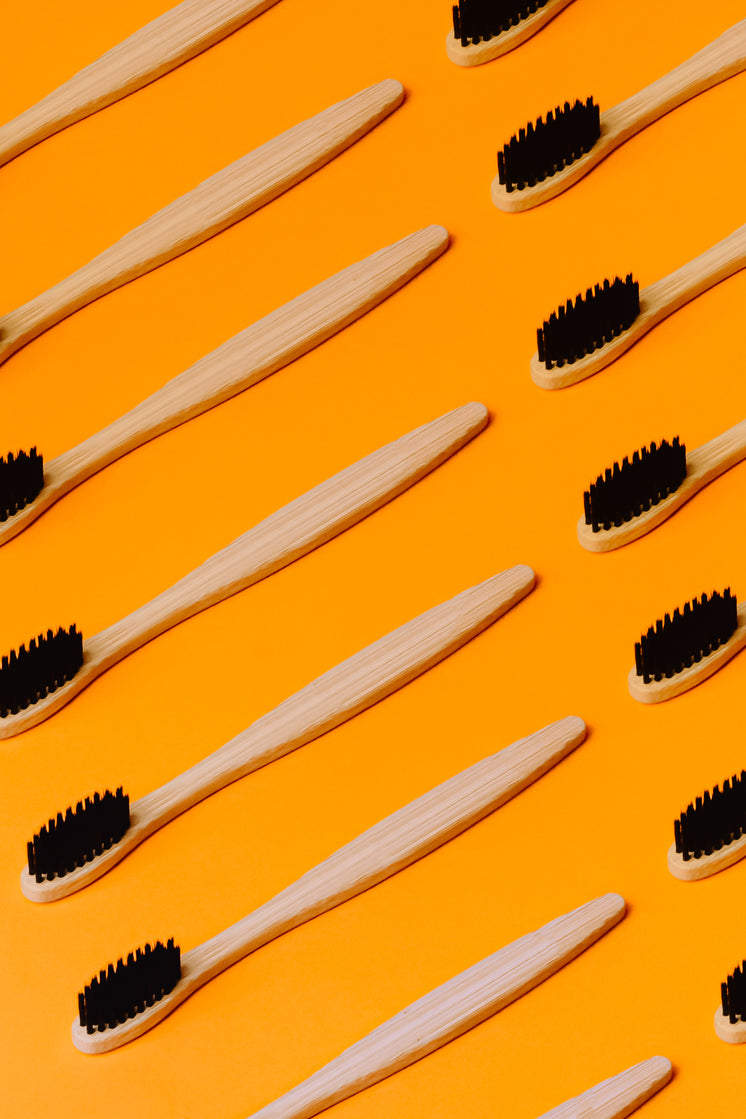
댓글목록
등록된 댓글이 없습니다.